Case Study: Deep Lane Storage with Push Back Flow Racking
Case Study: Deep Lane Storage with Push Back Flow Racking
Table of Contents
Introduction
Just because you have Last-In/First-Out (LIFO) inventory needs doesn’t mean you can’t benefit from a gravity flow rack system. Enter Push Back Flow Rack, which leverages pallet flow rails for high efficiency and added benefits over traditional push-back systems. At Storage Coordinators, we specialize in cutting-edge racking solutions, including Pushback and Pallet Flow Racks. This post explores the benefits of Push-Back Flow Racks, showcasing our expertise and real-world applications, particularly with a leading specialty egg producer.
What is Push-Back Flow Rack?
Push-Back Flow Racks handle Last-In/First-Out (LIFO) inventory needs while leveraging gravity flow benefits. Unlike traditional push-back racks using carts, these racks use pallet flow tracks for high-density storage and efficient handling. The system is designed to automatically replenish the pick face with the next pallet as pallets are removed from a lane. This ensures that the pick face is always stocked and the system is always optimized for efficiency.
Key Benefits of Push-Back Flow Rack
- High-Density Storage: Stores up to 12+ pallets deep, optimizing space.
- Low Profile Design: Maximizes vertical storage without sacrificing accessibility.
- Versatility: Suitable for various pallet sizes with wheeled or roller tracks
- LIFO Inventory Rotation: Ensures efficient LIFO rotation with smooth pallet movement.
- Flexibility: Converts to pallet flow racks if inventory needs change.
- Single Aisle Operation: Requires only one aisle, improving floor space utilization.
Case Study: Deep Lane Storage for Specialty Egg Producer
A leading specialty egg producer, partnering with approximately 160 individual Mennonite family farms, collaborated with Storage Coordinators to design a Push-Back Flow Racking system for storing egg carton pallets. Initially, the customer was block stacking all their pallets and double-stacking them, which caused issues with efficiency and safety. Their main requirements were to gain 300 pallet positions for increased storage, better cube utilization, and improved efficiency. Storage Coordinators successfully met all their requirements with this project.
During the design phase, we received a dozen of their pallets for live testing. We built a test lane to evaluate various pitches, pallet flow track types, and 2-rail vs. 3-rail configurations. Proper testing of customer pallets is crucial, and Storage Coordinators goes to great lengths to ensure a seamless installation. Testing confirmed that a 3-rail pallet flow lane with a 1-2-1 configuration (single-double-single) provided the best flow. The lane pitch was set at ½” per foot, allowing pallets to be pushed back easily without undue strain on the forklift and flow forward smoothly when the front pallet was removed, even after sitting in the lane for extended periods. The pallet loads were flush with little to no overhang, ensuring unimpeded flow.
By adding the pushback system, we increased the capacity with 3 flow levels high and allowed for SKU selectivity for each lane, enhancing efficiency and organization.
System Specifications
- 3 Deep, 8 Deep, and 10 Deep Push-Back Flow Racking
- 3-rail pallet flow with 1.9″ diameter steel skatewheel in a Single-double-single configuration
- GMA pallets: 40″ x 48″ x 85″, 800 lbs, and various other pallet sizes
- Pallet condition: very good
- ½” per foot pitch
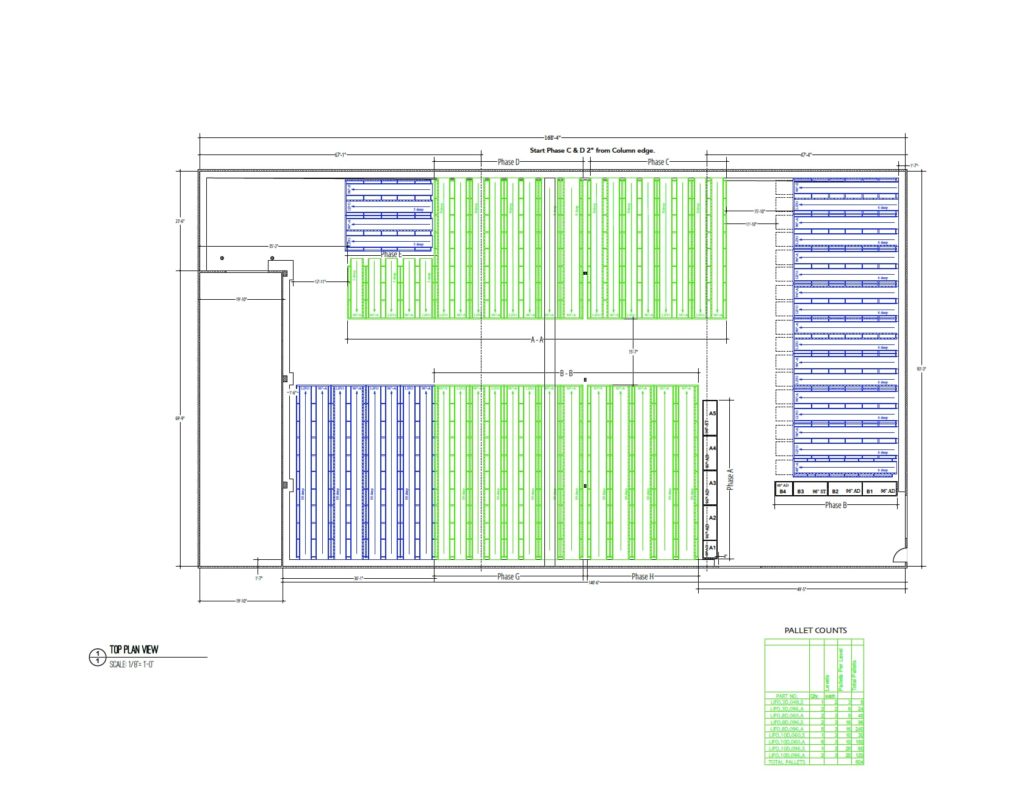
Benefits and Results
- Increased Storage Capacity: Added over 300 more pallet positions of storage versus block stacking on the floor two pallets high.
- Handling Various Pallet Sizes: Accommodates different-sized pallets, improving operational flexibility.
- SKU Management: Each flow level can hold a different SKU preventing the issues caused by stacking different SKUs on the floor.
- Improved Safety: Forklift drivers do not need to drive in and out of stacked boxes, reducing damage risk and increasing safety. This minimizes the chance of pallets toppling over, which can cause injuries and costly accidents.
- High-Density Storage and Efficient LIFO Inventory Management: 804 total pallet positions stored efficiently and safely.
Forklift Operator Safety Tips for Gravity Flow Systems
Proper training for forklift operators is crucial to ensure the safe and efficient use of gravity flow racking systems. The forklift operators who previously managed double stacking these pallets at the egg facility were highly skilled and similar precision is needed for operating push-back flow racks and other gravity flow racking. Here are some key safety tips:
- Inspect Loads for Loose Plastic Wrap: Loose plastic wrap can get caught in the rollers, causing damage and safety hazards.
- Center the Load on Roller Rails: Ensuring the load is centered prevents tipping and ensures smooth flow.
- Properly Raise and Place the Load: Carefully raise the load above ramp stops without striking the level above.
- Control Pallet Flow Speed When Unloading: Back out slowly to control the speed of pallets flowing forward, ensuring safety and preventing accidents.
These safety measures are essential for maintaining the integrity of the storage system and ensuring the safety of the warehouse environment, particularly in high-density storage scenarios like those implemented for the specialty egg producer.
The Power of Gravity Flow
Gravity flow racking systems enhance warehouse efficiency by reducing mechanical assistance and minimizing errors. At Storage Coordinators, we design and implement these solutions to meet diverse needs.
Conclusion
Push-Back Flow Racks offer a superior solution for LIFO inventory with high-density storage and operational efficiency. Contact Storage Coordinators for a free consultation to see how these systems can transform your warehouse operations.
Choosing the Right Storage System for Your Warehouse
Selecting the right pallet rack system for your business can be daunting due to significant capital expenditure and numerous variables in design and function. It’s crucial to conduct thorough research and seek expert advice to make an informed decision aligned with your business objectives, storage requirements, and budget. To help you find the best storage solution for your unique needs, let’s start by setting you on the right track. Refer to the table below for an at-a-glance comparison of different storage solutions to determine what best fits your space and budget. This table helps simplify some complex data and provides some rules of thumb. The cost per pallet position below is intended solely for ROM (rough order of magnitude) or high-level budgetary estimates for easy cost comparison. Keep in mind that prices consistently fluctuate with the price of steel, supply and demand, and many other factors.
To get an approximation for installation costs, installation costs typically range between 15% and 40% of the equipment cost depending on the type of warehouse racking system and several other factors. Selective pallet rack installation costs may range between 15% to 25% of equipment costs where a high-density dynamic storage system like Push-back racking or Pallet Flow racking may range between 25% to 35% of equipment costs. For the most accurate pricing, please consult with a material handling systems expert at Storage Coordinators.
Type of Racking | Cost per pallet position (est.) | Storage depth per lane | Inventory level per SKU | All loads accessible | Storage/Retrieval throughput | FIFO retrieval possible | Vertical honeycomb loss |
---|---|---|---|---|---|---|---|
Block Stacking | – | 2-10 | > 5 | No | Good | Yes | Yes |
Single Deep | $75 – $200 | 1 | < 3 | Yes | Good | Yes | No |
Double Deep | $80 – $200 | 2 | > 5 | No | Average | No | No |
Drive In | $200 – $400 | 5-10 | ≥ 20 | No | Average | No | Yes |
Drive Through | $200 – $400 | 5-10 | ≥ 20 | No | Average | Yes | Yes |
Push Back | $250 – $500 | 2-12* | 3-10 | No | Good | No | No |
Pallet Flow | $375 – $500 | 2-20 | 3-10 | No | Excellent | Yes | No |
Mobile Racks | – | 1 | < 3 | Yes | Poor | Yes | No |
Contact Us
FILL OUT THE FORM BELOW AND OUR STORAGE EXPERTS WILL GET BACK TO YOU WITHIN 1 BUSINESS DAY.